Tube filling machines play a critical role in industries such as cosmetics, pharmaceuticals, and food production. These machines ensure products are accurately filled and sealed in tubes for safe packaging. However, over time, wear and technical issues can disrupt operations, causing inconsistent fills, leaks, or seal failures. This comprehensive blog provides a detailed checklist for tube filling machine maintenance to identify common issues and prevent downtime. With Stelda – Wimco’s Tubefill Care+ program, all maintenance or repair needs identified during audits can be addressed swiftly, keeping your machine in peak condition.
Introduction: Why Regular Tube Filling Machine Maintenance is Crucial
Conducting regular maintenance of tube filling machines is essential to avoid operational disruptions and maintain consistent product quality. Misalignments, worn-out components, or clogs can lead to inefficiencies that escalate into costly downtime. Routine maintenance ensures every component—sealing jaws, nozzles, sensors—is functioning optimally. With high-speed production lines, even small oversights can result in significant product losses. Stelda – Wimco’s Tubefill Care+ program specializes in addressing maintenance needs, providing tailored services to keep your operations running smoothly.
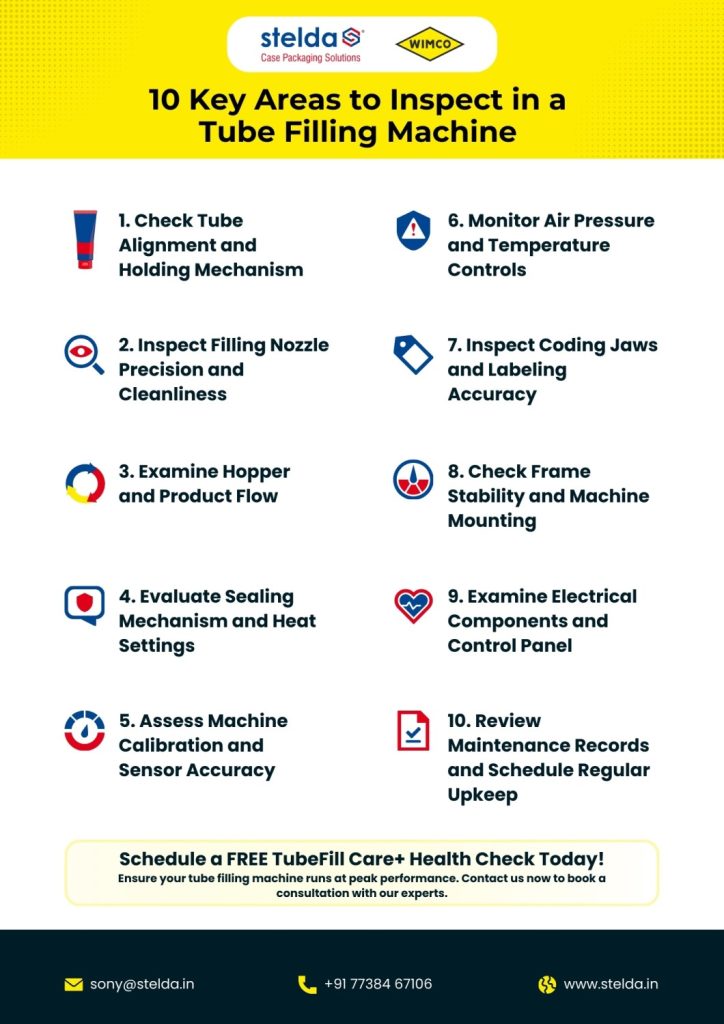
1. Check Tube Alignment and Holding Mechanism
Proper tube alignment is critical for accurate filling and sealing. Misaligned tubes can lead to product wastage and failed seals. During tube filling machine maintenance, ensure the holders grip the tubes securely and synchronize with the machine’s speed. Replace worn-out holders promptly to avoid disruptions.
2. Inspect Filling Nozzle Precision and Cleanliness
The nozzles are central to the filling process. Irregular fills or clogs in the nozzle can affect product dosing accuracy. Clean nozzles regularly and replace worn parts as needed. Nozzle integrity ensures the machine dispenses precise amounts during each fill cycle, a core focus of tube filling machine maintenance.
3. Examine Hopper and Product Flow
The hopper holds product before filling and impacts flow efficiency. Inspect for residue buildup, which can obstruct flow. Regularly clean the hopper to ensure smooth dispensing. Proper hopper care is vital for maintaining tube filling machine efficiency and preventing downtime.
4. Evaluate Sealing Mechanism and Heat Settings
Seals are critical for product integrity. Inspect heat settings to ensure sealing elements are functioning correctly. Poor heat distribution can result in weak seals. Routine maintenance of sealing mechanisms, including hot air and ultrasonic sealers, is crucial for efficient tube filling machine operations.
5. Assess Machine Calibration and Sensor Accuracy
Sensors regulate tube placement and fill levels, making calibration essential during maintenance audits. Misaligned sensors can lead to overfills or underfills. Regularly test sensor accuracy to ensure precise operations and seamless production.
6. Monitor Air Pressure and Temperature Controls
Machines using compressed air-driven seals rely on consistent air pressure. Inspect air pressure and temperature settings during tube filling machine maintenance to ensure they meet material-specific requirements. Inconsistent pressure can compromise seal strength, leading to leaks.
7. Inspect Coding Jaws and Labeling Accuracy
Automated machines imprint production details onto tubes. Misaligned coding jaws produce unreadable or inconsistent markings, affecting traceability. Ensure labeling mechanisms are functioning perfectly to uphold compliance standards.
8. Check Frame Stability and Machine Mounting
A stable machine frame ensures smooth operations. Loose frames can result in vibration, misalignments, and inconsistent fills. As part of your tube filling machine maintenance checklist, inspect the frame for wear or corrosion.
9. Examine Electrical Components and Control Panel
Electrical systems manage fill volume, speed, and temperature. Inspect all components for faults, loose connections, or moisture buildup. Reliable control panels ensure efficient operations and reduce downtime.
10. Review Maintenance Records and Schedule Regular Upkeep
Reviewing past maintenance logs reveals recurring issues, such as frequent nozzle replacements. Establish a proactive maintenance schedule to prevent sudden breakdowns. Stelda – Wimco’s Tubefill Care+ program offers preventive services tailored to production needs, ensuring your equipment runs efficiently.
Conclusion: Trust Stelda – Wimco’s Tubefill Care+ for Comprehensive Maintenance
Proactive maintenance is the key to maximizing efficiency and minimizing downtime in tube filling machines. By following this detailed checklist, operators can identify issues early, ensuring smooth operations and consistent product quality. Stelda – Wimco’s Tubefill Care+ program provides expert support for machine repairs and maintenance, helping you optimize your production lines. Contact us today to explore our tailored services and keep your tube filling machines in top condition.
Conclusion: Ensure Optimal Performance with Stelda – Wimco’s Tubefill Care+ Program
Regular audits are essential for identifying and addressing issues in tube filling machines, thereby ensuring consistent quality and performance. By following this checklist, operators can catch potential issues early, reducing downtime and enhancing productivity. Stelda- Wimco’s Tubefill Care+ program provides expert maintenance, repairs, and support, ensuring that your tube filling machines operate smoothly and efficiently. Through Tubefill Care+, you can minimize disruptions, prolong equipment lifespan, and maintain the highest standards in tube filling and sealing.
Would you like to explore Wimco’s Tubefill Care+ program and see how it can support your maintenance needs? Contact us today to learn more.
Authored by
Mr. Samir Limaye (Director – Wimco)
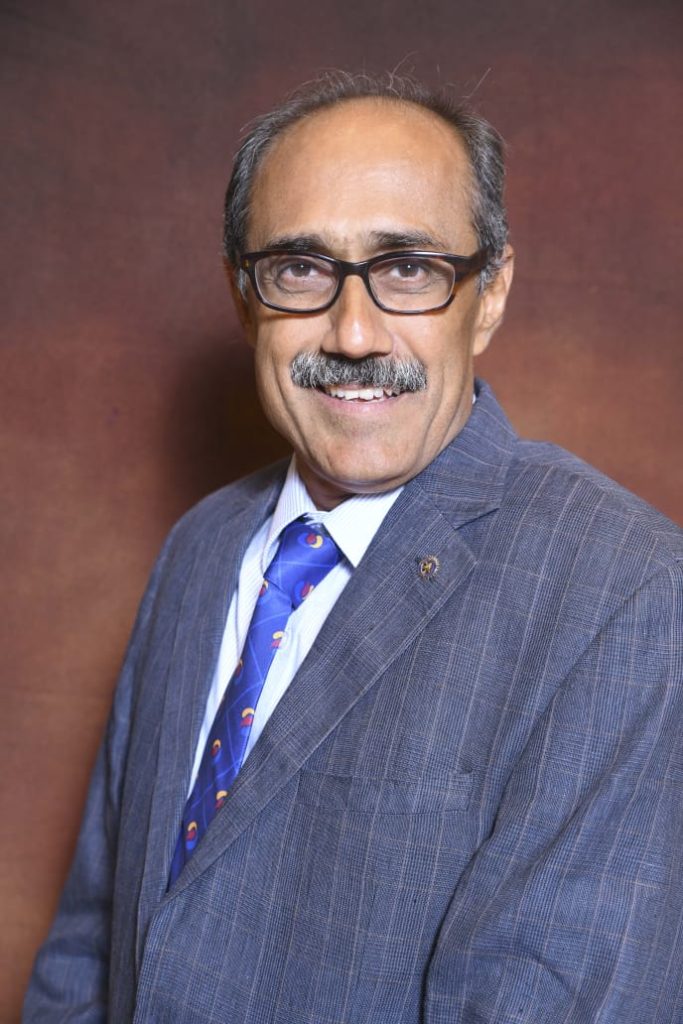
Stay ahead of the curve in the world of packaging!
Follow Stelda on Facebook, LinkedIn, and YouTube for the latest industry updates, innovative solutions, and expert tips to optimize your production.