When pharma-grade precision was compromised, Wimco by Stelda restored it in record time.
🏭 The Challenge
At Leben Laboratory, Akola, Maharashtra, a GAN 120 Double Head Tube Filling Machine — supplied earlier by WIMCO — faced filling inconsistencies after introducing a new SKU with very small grammage.
To adapt to this SKU, Leben had approached an external agency to fabricate a change part suitable for small tube filling. Unfortunately, this off-spec change part failed to perform, resulting in misalignment during filling and increased rejection rates.
This critical issue was responsible for filling 5 gm tubes. The problem was severe, with up to 15% of production facing rejection due to filling inaccuracies ranging from underfills to overfills, far from the stringent standards required in pharmaceutical production.
Root Cause: Incorrect Change Parts and Mismatched CAM
On inspection, Wimco by Stelda’s Tube Fill Care+ team swiftly diagnosed the problem:
❌ Mismatched CAMs and
❌ Non-OEM change parts that disrupted tube alignment and fill precision.
Leben had unknowingly installed off-market spare parts, which failed to meet OEM specifications for their GAN 120 machine.
The Result: Inconsistent fill volumes, GMP non-compliance, and higher rejection rates reduced overall productivity.
📣 The Response
When Leben saw Wimco by Stelda’s Tube Fill Care+ campaign, they immediately sought assistance. Our engineer, Naresh Sinhalkar, quickly reached the site, diagnosed the issue, and initiated a 48-hour resolution. What followed was a rapid, precision-driven turnaround—both CAMs were replaced, and the machine was fully operational within 48 hours, including post-repair trials. This success story highlights Wimco by Stelda’s expertise in precision tube filling solutions, service agility, and application knowledge in restoring GMP-compliant production standards.
🔧 The Solution: Correct CAM Replacement and Precision Calibration
To restore accuracy, Wimco by Stelda’s Tube Fill Care+ team redesigned the CAM mechanism and executed a meticulous repair plan:
- Genuine CAMs installed – perfectly aligned for 5 gm tubes. Both mismatched CAMs were removed and replaced with genuine Wimco by Stelda CAMs designed specifically for the new SKU requirement in their GAN 120 machine, ensuring tubes were lifted to the precise height required for accurate bottom filling.
- Precision Calibration: The machine was recalibrated for exact tube positioning, ensuring consistent fill volumes and GMP compliance.
- Rapid Turnaround: The entire repair process, including CAM replacement and post-repair trials, was completed within 48 hours, minimizing production downtime.
- Post-repair trials – ensured restored GMP-compliant filling
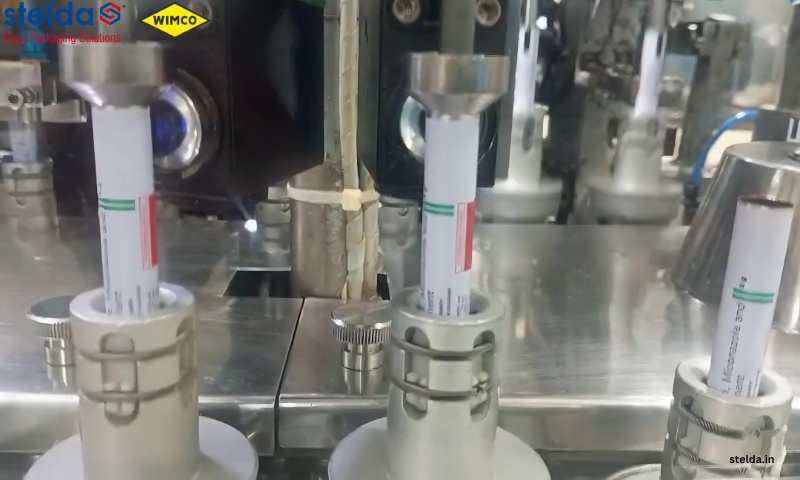
✅ The Results: Near-Zero Rejections and Optimized Production
The intervention delivered immediate and measurable improvements:
- Rejection Rates Plummeted: Fill accuracy was restored, reducing rejections to almost zero.
- Production Efficiency Improved: The machine operated at peak capacity, meeting GMP standards.
- Rapid Resolution: The entire repair process was completed in just 48 hours, including post-repair trials.
- Cost Savings: Reduced rejections minimized material waste and rework expenses.
- Regulatory Compliance: Consistent fill weights ensured GMP adherence and product quality.
Wimco by Stelda’s rapid response and expert troubleshooting prevented prolonged downtime, enabling a swift resolution.
💡 What We Learned
🔹 Use of off-market parts can disrupt precision
🔹 CAM design must match tube size and specs
🔹 Regular calibration ensures consistent quality
Why Precision Tube Filling Solutions Matter in Pharma
In pharmaceutical packaging, precision tube filling technology is essential for maintaining product integrity and meeting GMP requirements:
- Exact Dosage: Prevents air entrapment, ensuring accurate fill weights as per GMP Annex 1 guidelines for contamination control.
- Product Stability: Reduces air exposure, preserving the stability and shelf life of sensitive formulations, aligning with ICH Q8 (R2) guidelines for pharmaceutical development.
- Uniform Consistency: Guarantees product uniformity across batches, essential for GMP Part 211.110 requirements on process controls.
- Zero Wastage: Ensures complete dispensing, minimizing product loss.
- Equipment Qualification: Regular validation and calibration, as mandated by GMP Annex 15, ensure the machine operates within compliance parameters.
By restoring bottom filling accuracy, Wimco by Stelda’s Precision Tube Filling Solutions program ensured consistent, compliant production at Leben Laboratory.
WIMCO GAN 120: Powering Precision in Tube Filling
At the core of this success was the WIMCO GAN 120 Double Head Tube Filling Machine, renowned for its high-speed, precision-filling capabilities. Its standout features include:
- High-Speed Dual-Head Operation: Fills up to 120 tubes per minute, maximizing productivity.
- Tail-Free Filling: Ensures zero wastage with ±1% fill accuracy, meeting stringent GMP requirements.
- Versatile Tube Compatibility: Handles laminated, aluminum, and co-extrusion tubes with ease.
- Customizable Fill Range: Flexible filling from 1.5 to 250cc, catering to various product volumes.
The GAN 120’s reliability and adaptability played a pivotal role in restoring Leben Laboratory’s production efficiency.
Beyond the Fix: Long-Term Benefits of Precision Tube Filling Solutions
The Precision Tube Filling Solutions program delivered sustained value beyond the immediate fix:
- Extended Machine Life: Genuine Wimco by Stelda parts and precise calibration reduced wear and tear, extending the machine’s lifespan.
- Cost Optimization: Fewer rejections and reduced downtime resulted in significant cost savings.
- GMP Compliance: Accurate filling ensured consistent adherence to regulatory standards.
- Reliability of OEM Parts: The case highlighted the risks of using off-market parts, which compromise performance and increase operational costs.
- Operational Confidence: Leben gained the confidence of having a fully optimized machine with guaranteed precision.
🔍 Why WIMCO by Stelda Stands Out
- ✅ Rapid response through Tube Fill Care+
- ✅ In-house CAM engineering expertise
- ✅ Strong knowledge of pharma-grade filling standards
- ✅ Genuine OEM parts = long-term performance
- ✅ Support for legacy and current installations
🤝 Wimco by Stelda Tube Fill Care+: Your Partner in Precision Tube Filling Solutions
We help manufacturers like Leben not only fix issues but also future-proof their tube filling operations.
At Wimco by Stelda, we go beyond machine repairs—we maximize efficiency, accuracy, and longevity. The Precision Tube Filling Solutions Tube fill care+ program is a testament to our commitment to service excellence and customer success, helping pharma manufacturers maintain GMP compliance and production consistency.
If you’re facing filling inaccuracies, rising rejection rates, or frequent downtime, trust Wimco by Stelda’s Precision Tube Filling Solutions Tube fill care+ program for a rapid, reliable solution.
Need better accuracy, faster service, or advice on upgrades?
Reach out to WIMCO by Stelda’s Tube Fill Care+ team — we’re ready when you are.
👉 Follow us on social media to explore more industry success stories and stay ahead of pharma packaging trends.