How Tube Filling Machine Alignment Affects Your Bottom Line – And How to Fix It
Did you know? A misaligned tube filling machine can cause up to a 15% increase in product waste, disrupt seal integrity, and lead to regulatory non-compliance in industries like pharmaceuticals and cosmetics.
Tube filling machine alignment isn’t just about aesthetics—it’s a fundamental factor in ensuring operational efficiency, product quality, and compliance. A minor misalignment can:
✔ Reduce filling precision, causing overfilled or underfilled tubes.
✔ Compromise seals, leading to leaks and contamination risks.
✔ Slow down production, forcing operators to make constant manual adjustments.
✔ Cause rejection of final products, impacting your bottom line.
In this guide, we’ll break down the causes, impact, and solutions for tube filling machine alignment issues and provide a technical, in-depth troubleshooting checklist.
Why Tube Filling Machine Alignment Matters
In pharmaceutical, cosmetic, and food manufacturing, tube filling involves precise operations:
- Tube Orientation: Tubes must be properly positioned before entering the filling station.
- Filling Accuracy: The product must be dispensed centrally without excess residue.
- Sealing Precision: The tube must align exactly with the sealing jaws to ensure an airtight, tamper-proof seal.
Even 0.5mm misalignment can lead to product defects, making tube filling machine alignment a critical factor in maintaining industry standards like:
- GMP (Good Manufacturing Practices)
- FDA Regulations for Pharmaceuticals & Cosmetics
- ISO 9001 Manufacturing Standards
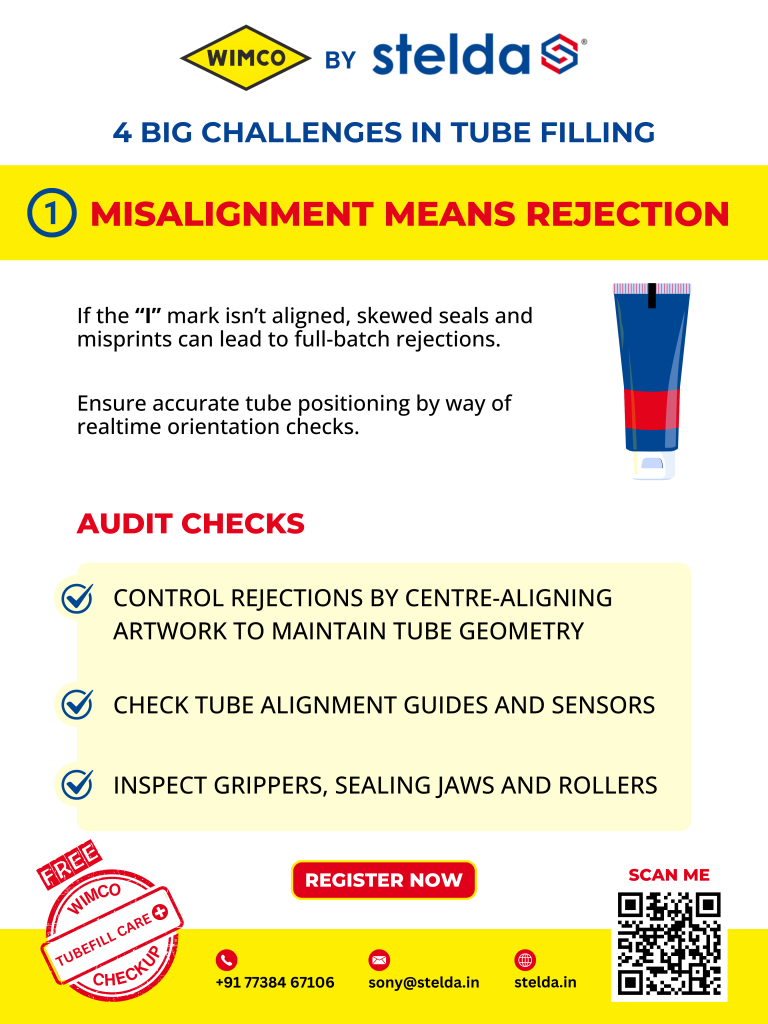
Common Causes of Tube Filling Machine Misalignment
1. Inconsistent Tube Feeding Mechanism
- What happens?
- Tubes enter the filling system at an incorrect angle, leading to improper positioning at the filling station.
- The tube clamp mechanism fails to hold tubes securely, causing shifts during the fill cycle.
- Solution:
✅ Ensure the tube loading carousel is calibrated to match tube dimensions.
✅ Inspect gripping mechanisms for wear and replace faulty clamps.
2. Calibration Errors in Sensor Systems
- What happens?
- Optical and mechanical sensors misread tube positions, leading to misalignment errors in high-speed production.
- Inconsistent fill levels due to incorrect sensor detection.
- Solution:
✅ Conduct automated sensor recalibration weekly.
✅ Use AI-powered detection to optimize real-time tube positioning.
3. Worn-Out Tube Positioning Mechanisms
- What happens?
- Mechanical guides, clamps, and rotary plates degrade over time, causing minor shifts that disrupt tube alignment consistency.
- Solution:
✅ Replace grippers, servo motors, and guide rails at predefined maintenance intervals.
✅ Switch to servo-driven tube positioning systems for enhanced precision.
4. Vibration and External Disturbances
- What happens?
- Factory vibrations or unstable floor mounting can slightly alter alignment precision, especially in high-speed fillers.
- Solution:
✅ Secure the machine with anti-vibration mounts.
✅ Use real-time torque monitoring for rotary components.
Troubleshooting Tube Filling Machine Alignment Issues
Step 1: Check Tube Orientation Before Filling
🔍 Inspect the tube carousel – are tubes aligned correctly before entering the filling station?
🔍 Adjust tube holders – confirm they grip tubes firmly but not too tightly to prevent shifting.
Step 2: Validate Nozzle-to-Tube Alignment
🔍 Measure fill accuracy – a variance of more than ±1% indicates alignment drift.
🔍 Check nozzle travel path – ensure it lowers precisely into the tube’s center.
Step 3: Analyze Seal Integrity & Tube Position
🔍 Evaluate crimping/sealing mechanisms – heat jaws or ultrasonic sealing heads must be centered for airtight seals.
🔍 Inspect tube rotation – slight tube movement during sealing can cause defective seals.
7 Advanced Strategies to Maintain Tube Filling Machine Alignment
1. Upgrade to Servo-Controlled Tube Alignment Systems
📌 Why? Traditional pneumatic systems cause slight variations in tube positioning. Servo systems ensure high-precision alignment.
2. Use High-Resolution Camera Sensors for Tube Orientation
📌 Why? AI-powered cameras can detect misalignment in real time and automatically adjust tube positioning.
3. Implement Automatic Recalibration Software
📌 Why? Auto-calibration systems self-adjust mechanical offsets, reducing manual intervention.
4. Adopt Predictive Maintenance for Positioning Mechanisms
📌 Why? AI-based maintenance systems detect wear in alignment guides before failure.
5. Optimize Tube Loading & Conveyor Synchronization
📌 Why? Poor conveyor-to-feeder synchronization distorts tube orientation before filling.
6. Adjust Machine Mounting for Maximum Stability
📌 Why? Unstable machine bases affect precision, especially at higher production speeds.
7. Leverage Smart AI Feedback for Operator Training
📌 Why? AI-guided machine learning algorithms help operators detect early alignment issues.
Maximizing Efficiency with Precision Tube Filling Machine Alignment
A perfectly aligned tube filling machine leads to:
✅ Higher production efficiency – reduced rejections and faster cycles.
✅ Minimal product wastage – precise alignment ensures accurate fills.
✅ Stronger brand reputation – visually perfect, defect-free packaging.
🚀 The future of tube filling is precision-driven! By leveraging advanced alignment systems, AI detection, and servo-controlled mechanisms, manufacturers can eliminate inefficiencies and boost overall output.
💡 Want expert alignment solutions? Contact us today for precision engineering upgrades!📢 Follow us on LinkedIn, Facebook & YouTube for more manufacturing insights!