The Silent Threat of Product Contamination in Tube Filling Machines
The world of consumer goods relies heavily on precise and efficient tube filling machines. From pharmaceuticals and cosmetics to food and industrial products, these machines ensure consistent product delivery in a convenient format. Maintaining the highest hygiene standards is critical in these industries. One significant challenge is product contamination during the tube filling process, which can lead to compromised product integrity, regulatory penalties, and health risks for consumers. This blog highlights the causes, impacts, and preventive measures against contamination, emphasizing the importance of disassembling and sterilizing specific modules in a separate location for thorough cleaning.
What is Product Contamination in Tube Filling?
Contamination occurs when foreign substances or residual materials from prior batches compromise the quality of the product. In tube filling machines, contamination risks are often associated with:
- Residual buildup in filling nozzles or tanks.
- Foreign materials, such as dust or debris, entering the filling system.
- Inadequate cleaning and maintenance protocols.
For instance, in pharmaceutical production, even minute contaminants can lead to regulatory actions by authorities like the Central Drugs Standard Control Organization (CDSCO) or international regulators like the FDA.
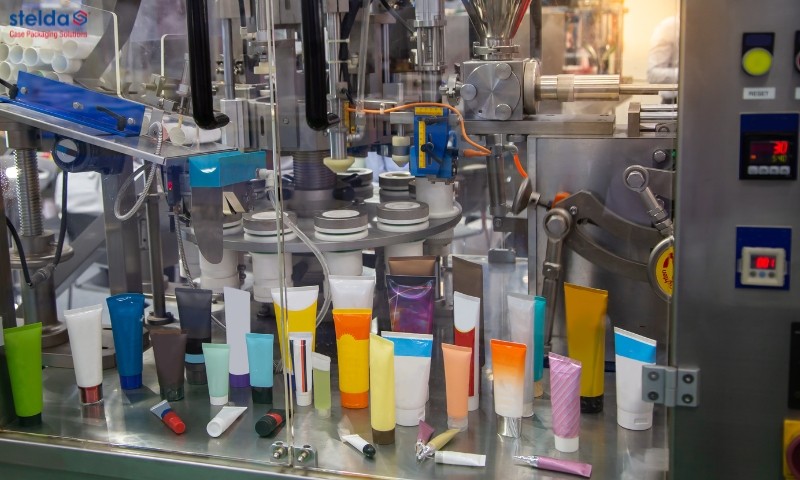
Causes of Product Contamination in Tube Filling Machines
- Inadequate Cleaning Procedures
- Manual cleaning can overlook intricate machine parts, leaving behind residues.
- Automated systems might fail without proper validation or use of suitable cleaning agents.
- Residual Buildup in Key Components
- Nozzles and tanks accumulate residues from viscous products, leading to cross-contamination between batches.
- Foreign Materials in the System
- Poorly maintained environments introduce dust, debris, or microorganisms into the production line.
- Machine Wear and Tear
- Worn seals, valves, or other components compromise the machine’s ability to maintain sterility.
Impact of Product Contamination in Tube Filling Machines
- Regulatory and Legal Consequences
- Non-compliance with GMP or CDSCO standards can result in penalties, product bans, or revoked licenses.
- Contamination may necessitate product recalls, damaging brand reputation.
- Health Risks
- Contaminated pharmaceutical or cosmetic products pose severe risks, from allergic reactions to life-threatening complications.
- Financial Losses
- Recalls, waste, and halted production lines contribute to significant financial setbacks.
- Operational Downtime
- Unplanned maintenance due to product contamination in tube filling machines disrupts production schedules.
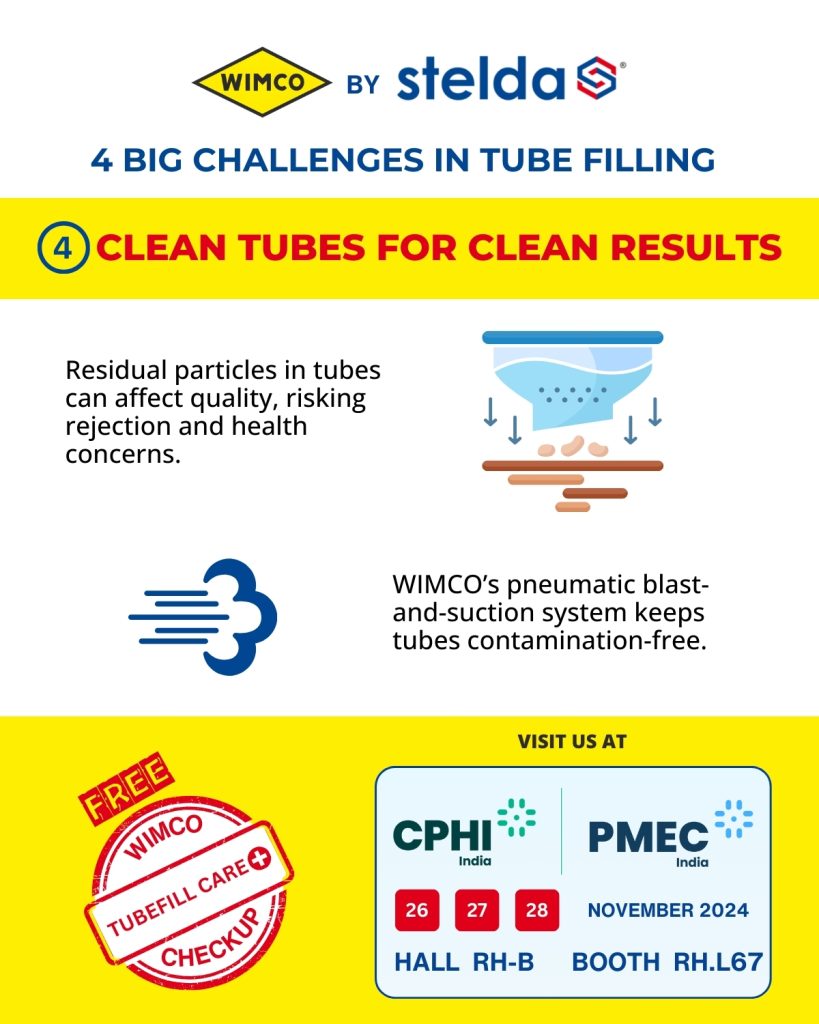
Best Practices for Cleaning Tube Filling Machines
- Establishing a Cleaning Schedule
- A well-defined cleaning schedule is paramount for ensuring that tube filling machines remain contaminant-free. Cleaning should occur:
- Before production starts
- After each production run
- When switching between different products or batch numbers
- Regular cleaning intervals help prevent the accumulation of residues that could lead to product contamination in tube filling machines
- A well-defined cleaning schedule is paramount for ensuring that tube filling machines remain contaminant-free. Cleaning should occur:
- Use of Appropriate Cleaning Agents
- Selecting the right cleaning agents is critical. Non-toxic, food-grade cleaners that comply with industry standards should be used to clean all parts of the filling machine. The effectiveness of these agents can significantly impact the cleanliness of the equipment.
- Comprehensive Cleaning Procedures
- Cleaning procedures should include:
- Disconnecting power sources and isolating machines from product sources.
- Disassembling removable parts such as nozzles and hoses for thorough cleaning.
- Using brushes and scrubbing tools tailored for different surfaces to ensure all residues are removed.
- Rinsing all components with clean water to eliminate any remaining cleaning agents before reassembly.
- Cleaning procedures should include:
- Staff Training and Compliance
- Training personnel on proper cleaning techniques and hygiene practices.
- Employees must be familiar with standard operating procedures (SOPs) related to equipment cleaning and sanitation protocols
- Regular training sessions can enhance compliance and reduce the likelihood of human error leading to contamination.
- Ensure Regular Machine Maintenance
- Schedule inspections to identify and replace worn parts before contamination occurs.
- Maintain detailed records of cleaning and maintenance to comply with regulatory audits.
- Disassemble and Clean Modules Separately
- Disassemble components such as nozzles and tanks at the end of each production batch.
- Clean and sterilize them in a designated area to prevent cross-contamination. Detailed steps are outlined below.
- Advanced Technologies in Filling Machines
- Use machines with contamination prevention features, such as precision nozzles, HEPA filters, and automatic sealing mechanisms.
- Environmental Controls
- Employ air filtration systems to maintain cleanroom conditions.
- Train staff regularly on hygiene protocols and contamination risk management.
Cleaning and Sterilizing Modules in a Separate Location
- Pre-Cleaning Preparation
- Shut down the machine and isolate the components for cleaning.
- Ensure operators wear Personal Protective Equipment (PPE) to maintain sterility.
- Disassembly and Transportation
- Carefully disassemble the module, such as the nozzle or tank, following the manufacturer’s guidelines.
- Transport these components in sterile containers to the designated cleaning area.
- Cleaning Process
- Remove visible residues using warm water and industry-approved detergents.
- For stubborn residues, use ultrasonic cleaners to ensure precision.
- Sterilization
- Sterilize metal parts in an autoclave and use chemical sterilants or UV treatment for sensitive components.
- Ensure all parts are thoroughly dried and stored in sterile packaging.
- Reassembly
- Reassemble sterilized components according to standard operating procedures.
- Perform functionality and cleanliness checks before reintegration into the production line.
Conclusion
Preventing contamination in tube filling machines is essential for maintaining product quality, customer safety, and regulatory compliance. By integrating advanced technologies, disassembling and cleaning modules separately, and adhering to rigorous hygiene protocols, manufacturers can minimize risks and ensure consistent, high-quality production. Explore innovative tube filling solutions at Stelda to enhance your production capabilities while ensuring contamination-free processes.
Stay ahead of the curve in the world of packaging!
Follow Stelda on Facebook, LinkedIn, and YouTube for the latest industry updates, innovative solutions, and expert tips to optimize your production.
FAQs
- Why clean modules in a separate area?
- Cleaning modules in a designated location reduces cross-contamination risks and ensures thorough sterilization.
- What are the best sterilization methods?
- Autoclaving for metal parts and UV or chemical sterilization for sensitive components are effective.
- How often should machines be cleaned?
- Machines should be cleaned after every batch and deep cleaned as per GMP schedules.