Seal integrity is critical in plastic tube packaging, ensuring that products are protected from leakage, contamination, and spoilage. However, maintaining seal integrity in tube filling machines can be challenging due to various technical issues. This guide explores the common causes of weak seals, how to optimize heat-sealing processes, and essential methods for testing seal strength, ultimately helping manufacturers uphold quality and safety in their packaging.
Why Seal Integrity Matters in Tube Packaging
In industries such as pharmaceuticals, cosmetics, and food, plastic tube packaging is favored for its convenience and durability. However, the effectiveness of this packaging heavily relies on seal integrity. Weak or incomplete seals can lead to product leaks, exposure to contaminants, and significant losses for manufacturers due to recalls and customer dissatisfaction. By understanding common tube sealing issues and optimizing sealing processes, manufacturers can achieve high-quality, reliable seals.
Common Plastic Tube Sealing Issues and Their Causes
Weak or incomplete seals in plastic tubes often stem from several technical factors. Recognizing these issues is the first step toward improving packaging quality.
- Weak Seals:
Weak seals are a primary concern, often caused by worn-out heating elements or misaligned sealing jaws. Worn heating elements struggle to deliver sufficient heat for proper bonding, leading to weak seals susceptible to tears and punctures.
- Misaligned Sealing Jaws
Misalignment of sealing jaws can lead to inconsistent pressure during the sealing process, resulting in weak seals that fail under pressure. Misalignment often occurs due to wear and tear in high-speed production environments and inadequate calibration, especially in fully automated tube filling machines. Misaligned jaws exert uneven pressure, resulting in inconsistent seal strength and potential leaks.
- Inadequate Heating and Faulty Heating Elements
Heat is crucial for creating a strong bond between tube layers, especially for plastic materials like polyethylene. When heating elements are worn out or unevenly heated, the seal may be insufficiently fused. Regular maintenance and inspection of heating elements are essential for consistent sealing. Choosing a machine with dependable heating elements, such as Wimco’s Tube Filling Machines, can help manufacturers maintain consistent heat application, which is essential for creating strong, leak-proof seals.
- Compatibility Issues with Tube Material
Plastic tube materials vary in their heat tolerance and sealing requirements. Using materials that are incompatible with the machine’s sealing settings can lead to seals that are either too weak or easily broken. Ensuring that tube materials are compatible with the machine’s sealing technology is vital for optimal performance. Wimco’s machines are designed to handle a wide range of materials, ensuring high-quality seals across various applications.
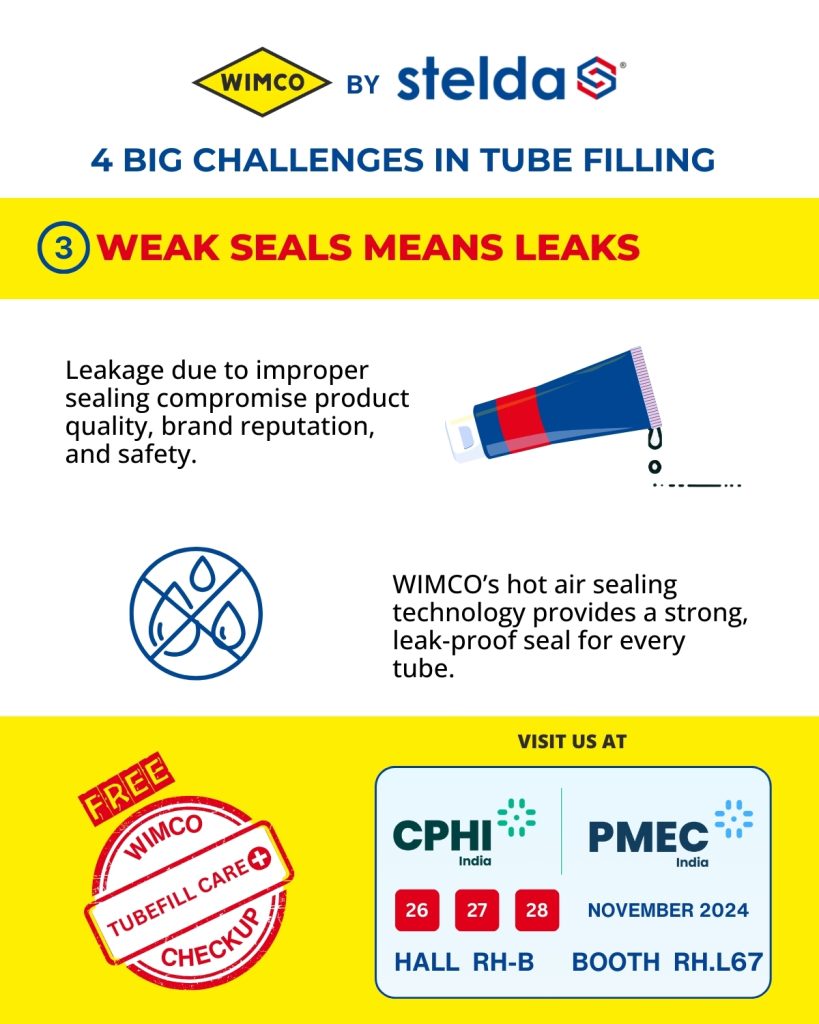
Optimizing Heat-Sealing in Tube Filling Machines
Achieving the ideal seal strength requires carefully calibrated heat, pressure, and timing. Here’s how manufacturers can fine-tune these factors for better sealing outcomes.
- Optimal Heat Settings for Various Materials
Different materials require specific heat settings. For example, polyethylene tubes need a higher temperature compared to laminate tubes to achieve an adequate seal. Many machines offer adjustable heat settings, allowing operators to fine-tune temperatures based on the material being processed. Wimco’s tube filling machines provide adjustable heat settings that allow operators to fine-tune temperatures based on the material, ensuring a high-quality seal every time.
- Control Over Pressure and Dwell Time
Applying sufficient pressure and controlling the dwell time (the time the sealing jaws stay closed) are critical for a strong bond. Too much pressure can damage the tube, while insufficient pressure weakens the seal. Manufacturers should regularly review their pressure settings and dwell times to match the tube material and product specifications. Wimco’s machines include customizable pressure controls to optimize seal quality, reducing the chances of tube damage or weak seals.
- Real-Time Monitoring of Sealing Parameters
WIMCO’s machines incorporate sensors that monitor temperature, pressure, and sealing time. Real-time data helps identify deviations and make automatic adjustments, ensuring consistency across large production volumes. This technology minimizes human error and enhances seal reliability.
Seal Integrity Testing Methods for Quality Assurance
- Burst Testing
Burst testing involves applying internal pressure to a sealed tube until it bursts, providing a measure of its strength. This method helps identify weak spots in the seal and ensures that the tube can withstand typical pressures encountered during shipping and handling.
- Vacuum Decay and Dye Penetration Tests
The vacuum decay method detects micro-leaks by monitoring pressure changes within a vacuum chamber. Dye penetration involves placing a dyed solution around the seal area to detect leaks. Both methods are valuable for non-destructive testing and can help identify tiny defects that could compromise product safety.
- Destructive vs. Non-Destructive Testing
Destructive tests, like burst testing, provide detailed insights into the strength of the seal but result in unusable products. Non-destructive testing, like vacuum decay, allows batch testing without product waste, making it a preferred option for quality control in large-scale production.
Best Practices for Routine Quality Control:
- Regular Inspections: Conduct visual inspections of the sealed tubes to identify any abnormalities like wrinkles, creases, or discoloration.
- Periodic Calibration: Ensure the sealing machine is calibrated regularly to maintain consistent pressure, temperature, and jaw alignment.
- Material Compatibility Testing: Periodically test the compatibility of new tube materials with the existing sealing process to prevent unexpected issues.
- Statistical Process Control (SPC): Implement SPC techniques to monitor key parameters and identify potential problems early on.
- Operator Training: Provide comprehensive training to operators on proper machine operation, maintenance, and troubleshooting.
Choosing the Right Plastic Tube Filling Machine
Selecting a suitable tube filling machine can significantly impact seal quality. Here are factors to consider when choosing equipment that enhances seal integrity.
- Types of Tube Filling Machines
- Fully Automatic Machines: They are ideal for high-volume production, as they streamline sealing processes from start to finish.
- Semi-Automatic Machines: They are useful for lower production volumes and allow more manual control over the sealing process.
- Manual Machines: They require manual operation for each tube, suitable for small-scale production or specific applications.
- Material Compatibility
Not all machines are compatible with every tube material. It’s crucial to select a machine capable of handling specific materials, such as plastic, laminate, or aluminum, without compromising seal quality. This reduces the risk of material-based tube sealing issues.
- Production Volume and Accuracy Needs
The scale of production directly influences machine choice. High-volume operations require machines capable of maintaining accuracy while achieving rapid throughput without compromising seal quality.
- Regular Maintenance and Support
Even with the best machines, regular maintenance is essential for reliable seal integrity. Wimco provides comprehensive support and access to replacement parts, ensuring minimal downtime, maintaining production quality and sustained seal integrity.
Ensuring Consistent Seal Integrity in Tube Packaging
Maintaining strong, reliable seals in tube filling machines is essential for product quality and customer satisfaction. By understanding common tube sealing issues, optimizing heat-sealing processes, and implementing rigorous testing, manufacturers can enhance their production quality and protect their products. Investing in the right tube filling machine and maintaining consistent testing and calibration processes are the keys to achieving reliable seal integrity in tube packaging.
Investing in high-quality WIMCO tube filling machines coupled with regular maintenance practices will yield long-term benefits in terms of product safety and brand reputation. Prioritizing these strategies are the key to achieve reliable seal integrity in tube packaging